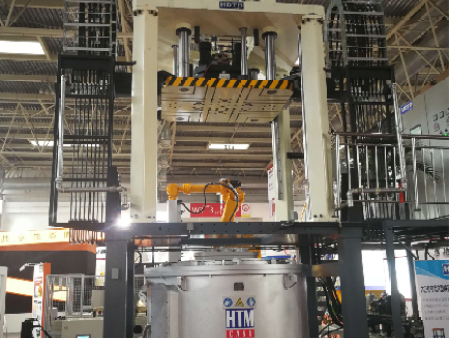
HDTD-3500 large casting machine Crucible shuttle is dedicated to chassis suspension system, multi-feeding port, shell, lightweight aluminum profile member design for big castings : nuke ,subframe ,arms new extra large high cleanliness class 坩埚 holding furnace Big Crucible ,clean metal Rigid multi-liter tube filling system software Multi risers little soft design For puring...
HDTD-3500 large casting machine Crucible shuttle
Committed to chassis suspension system, multi-feed port, housing, lightweight aluminum profile member design
For big castings : nuke ,subframe ,arms
New extra large high cleanliness grade 坩埚 holding furnace
Big crucible ,clean metal
Rigid multi-liter liquid tube filling system software
Multi risers little soft design For puring gate
High-precision working pressure automatic control system, hand-forging main parameter setting system software
High precision control process
Aluminum liquid floating control, warm lift pipe manipulation
Riser tube control
The supporting facilities will change the furnace and quickly change the furnace, and establish a high-precision abrasive refrigeration system that continuously produces and produces 47 channels of wind, water and fog water.
Shuttle furnace exchange little multi cooling
All-large digital servo motor hydraulic transmission system, environmental protection and energy saving
Digital servo hydraulic station
Low-pressure casting wheel machinery is usually classified according to the design method, and is habitually divided into general sand casting and special medium forging. Generally, sand casting includes several types of wet sand type, dry sand type, and organic chemical hard bottom sand casting. Special medium forging is different according to the design of raw materials, and can be divided into two categories: the category uses pure natural mineral sand as the key design raw materials, such as investment casting, shell forging, air pressure forging, mud forging, real forging , porcelain forging, etc.; the category uses metal materials as key metal casting materials, such as metal casting, centrifugal casting, continuous forging, working pressure forging, low pressure casting, etc.
Post-processing of castings carries out the whole process of quenching and tempering, plastic surgery, rust prevention and primary processing on the removed castings. Post-processing of castings is the final process flow for the production of foundry equipment.
The casting removal removes the casting from the metal mold, eliminates unnecessary parts other than itself, and polishes the entire process of polishing the inside and outside of the casting equipment. In the key work, there are cores and cores.
Forged non-ferrous metal alloys are used to cast non-ferrous aluminum alloys for castings and are a category in foundry equipment. The key is wrought alloy copper, cast aluminum alloy, forged magnesium alloy and so on.
The simulation of the castings looks like a machining process weapon or consumable item that produces a metal mold cavity. In order to ensure the production of a conforming cavity, the sample should have any compressive strength and bending stiffness.
The riser is additionally filled on the side or side of the casting equipment to prevent the casting from appearing as a disadvantage. In metal casting, the cavity of the riser is a vessel that stores liquid metal. [1]
The core box uses the core sand as a processing technology for forming a core. It can be made of wood, plastic, metal materials or other raw materials.