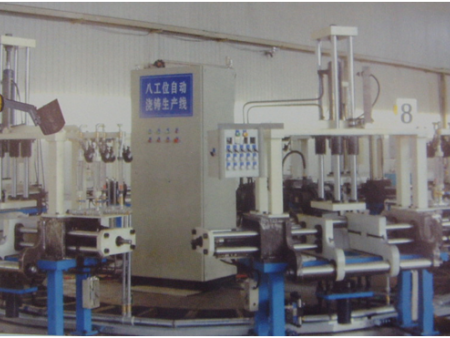
Gravity casting machine gravity casting refers to the processing technology of metal material liquid poured into the cavity of metal material under the effect of cosmic force to obtain the casting. The gravity casting in the theory includes sand casting, metal material casting, investment casting, lost foam casting, mud die forging, etc.; narrow gravity casting refers to metal material casting. Gravity casting machines usually refer to the establishment of metal material type force casting for opening, clamping and picking up equipment. Metal material type gravity casting machines are divided into two types, which are only tilting gravity casting machines and mobile gravity casting machines. The tilting gravity casting machine can establish the tilting and pouring of the grinding tool, which can reasonably improve the essence of the casting....
Gravity casting machine gravity casting refers to the processing technology of metal material liquid poured into the cavity of metal material under the effect of cosmic force to obtain the casting. The gravity casting in the theory includes sand casting, metal material casting, investment casting, lost foam casting, mud die forging, etc.; narrow gravity casting refers to metal material casting. Gravity casting machines usually refer to the establishment of metal material type force casting for opening, clamping and picking up equipment. Metal material type gravity casting machines are divided into two types, which are only tilting gravity casting machines and mobile gravity casting machines. The tilting gravity casting machine can establish the tilting pouring of the grinding tool, which can reasonably improve the essential quality of the casting, and is very suitable for the force casting of various kinds of casting parts such as the intake manifold.
Safety technical specifications Forging risk sources and multiple safety accidents Forging manufacturing has many processes, lifting and hoisting cargo volume, high temperature during processing, and causing various harmful substances and smoke, smoke and Noise and other characteristics, such as forging safety operations often cause burns, fire accidents, explosions and mechanical injuries and other safety accidents; another, it is also easy to cause radiant heat, poisoning, vibration and silicosis and other occupational health damage. Therefore, the safety of forging safe work is the most important for anti-fouling, heat insulation and mechanical damage. The following people will detail the safety common problems in accordance with the different process flow of forging safety operations.
Key point of operation
1. In the safe operation of sand mixing, the workers usually use the wheel-type sand mixer. The key risk of this type of machinery is that when the actual operation staff is running, the machine will reach out to remove the sand sample or view the sand. At the time, the hand is caught or dragged into the sand mixer, causing damage. Therefore, people should pay special attention to the following key points of operation when using the roller-type sand mixer:
(1) The equipment should be maintained and managed by a special person. Before driving, check all the way and make sure everything is normal before applying.
(2) After the sander is started, it is forbidden to dip the material by hand, remove the roller, and prohibit the sand sample from being taken by hand.
(3) When entering the maintenance and cleaning of the grinding plate, it is necessary to disconnect the switching power supply and set up special personnel to monitor. And on the high-voltage switchgear, the safety sign "Many people repair, prohibit reclosing" is hung.
(4) The sander needs a sampler, and the sander without a sampler must be sampled after shutdown.
(5) It is strictly forbidden to shovel the sand from the machine while the sander is working.
(6) Immediately remove the sand and articles scattered on the working environment to ensure the safety of the workers.
2. Design safety work
(1) Model design Safety work should pay special attention to the safety of lifting and hoisting transportation. It is absolutely forbidden to work conveniently under the hoisting object. It is reasonable to put the sand type on the stable and firm support frame to avoid falling objects. lethal.
(2) When making hand-made design and core making, pay special attention to avoid sand box, core box floor-standing lame, finger extrusion by sand box, steel nails in sand and other sharp copper pieces to cut hands and nails. Tired and other damage. In the actual operation, special attention should be paid to the method of transporting the sand box and the core box, wearing the safety shoes with firm upper, and separating the steel nails and the metal material fragments in the sand by the sieve residue or magnetic separation.
(3) The design of the sandbox is designed to avoid collapse and fall, and the total aspect ratio of the pallet is usually not more than 2m.
(4) When selecting the design of the pit design, it is necessary to know the water level line at the design position of the pit, to prevent the high temperature metal material liquid from exploding during the pouring, and to distribute the exhaust pipe hole so that the metal type bottom end steam The physical energy is successfully discharged.
(5) The ribs of the core iron and the sand box do not need to be exposed on the metal mold surface layer. Otherwise, because it is damp, the contact between the metal material liquids is most likely to cause “bonfire”, and the burn safety operation staff.
(6) When designing the equipment and designing the core, it is necessary to understand the characteristics and operating procedures of the equipment.
(7) When designing sand, the actual operation staff should wear hard-headed work shoes and maintain the concentration of mental essence. When actually operating the tamping machine, the hammer does not have to lie on the sole or box edge, the box belt, and the glue. On the mouth and exhaust port to prevent damage to sand quality and cause personal accidents.
(8) When designing the sand throwing design, the operators should cooperate with each other; there is no need to stack sand boxes and other objects around the hanging wall of the sand throwing machine; when the work is terminated, the wall should be tightly closed so that it cannot swing.
3. Sand type air dry safety operation
(1) When loading and unloading the furnace, it is necessary to have a special person to bear the commander. When loading and unloading the sand type (core), it is necessary to load and unload the average value, and it is not possible to adjust it on one side to prevent the vehicle from turning over.
(2) When loading the furnace, it should be ensured that the loading is stable, and the sand box stacking should be large and small, sorted one by one. Use the iron piece in the middle of the upper and lower left and right sand boxes to avoid skewing and shaking.
(3) When sanding (core) hoisting, special attention should be paid to the hoisting net weight, and the driving load should not be exceeded. Each hoisting sand type stipulates the same specification and model size, and can not be mixed.
(4) It is strictly forbidden to accumulate flammable materials and flammable materials around the fire door.
(5) It is forbidden to accumulate roadblocks around the mouth of the furnace and around the rails to ensure smooth driving.
(6) Wear a heat-insulating hood when adding coal or slag to prevent fire and heat from burning the face.
4. Pouring and pouring
(1) The pouring work should be worn with work clothes and safety goggles.
(2) Check the ladle, lifting ring and load-bearing beam with or without cracks; whether the mechanical equipment rotates and accurately locates the clamping device is not flexible, stable and reliable; the lining is firm and not tidal; The head is inseparable from the plug sleeve and does not cause leakage of molten steel.
(3) The safe passage of pouring should be smooth, no pits and bumps, no roadblocks, and prevent falling. The size of the hand-made lifting rack should be suitable, so that the center of gravity of the metal material liquid is placed under the ring sleeve to prevent the ladle from collapsing out of the lifting rack.
(4) Prepare in advance to solve the problem of the place where the molten metal material liquid is poured and the ingot mold (sand bed or iron mold).
(5) When lifting the ladle filled with iron (steel) water, pay special attention to not having to hit the iron (steel) trough and causing iron (steel) water to fall and splash. The pouring of molten iron should not be too full, and should not exceed 90% of the capacity to prevent spillage.
(6) The upper and lower boxes of the metal casting must be clamped or added with any net weight of the weight to prevent the box from being lifted and “running fire”.
(7) In the pouring, when the metal material liquid in the metal casting exceeds the necessary aspect ratio, the air is immediately ignited (ignition), and the flammable and non-flammable gas in the metal casting is discharged.
(8) If there is a serious "bonfire" during pouring, stop pouring first to prevent the metal material from splashing and causing burns and fire accidents.
(9) When casting metal type castings that cause harmful substances (such as sodium silicate flowing sand, dolomite sand, resin sand metal casting), it is necessary to pay attention to natural ventilation and avoid poisoning.
5. Falling sand, clearing
(1) The falling sand cleaning workers must do a good job of personal protection and understand the operating procedures of various falling sand removal machines.
(2) When casting parts are taken from the pile of castings, they should be taken from top to bottom to prevent the castings from collapsing and letting them die. Lifting equipment should be applied to the rolling of heavy extra large castings.